Vinyl Flooring

Vinyl Flooring:
Vinyl Flooring is defined as either resilient Vinyl sheet Floor covering or
resilient Vinyl tile Floor covering. Vinyl sheet Floor-covering is generally
available in either 6 ft (1.83 m) or 12 ft (3.66 m) widths and Vinyl Tiles
are generally 12 x 12 in (30.48 x 30.48 cm). Sheet goods are generally retailed
with no sticky backing. Thus, adhesives need to be purchased to adhere the
Flooring to underlayment. Vinyl Tiles may be purchased dry or with a
pressure-sensitive Glue backing protected by a paper covering that must be
removed by the installer.
Vinyl Sheet Flooring:
Vinyl sheet Flooring, particularly, varies in thickness and in manner decorated.
Thinner sheet Vinyl is 10-15 mils in thickness as opposed to longer wearing sheet
Vinyl that may be 25-30 mils thick. Patterns may be printed with a rotary press
or with large plates engraved intaglio with the design engraved below the
surface of the metal. Both printing methods impress a pattern on top of the Gel
Layer of Foam and underneath the wear Layer, rendering a relatively durable pattern.
Vinyl Floorings:
These Vinyl Floorings are preferred by many home owners for their ease of
installation—many do-it-yourselfers are able to install them with relative ease.
However, Vinyl sheet Floor Coverings that are 25-30 mils may difficult to handle
or install for the unskilled home owner. The Vinyl Tiles are far easier to install
and are the Vinyl Flooringing most often installed by the home-owner. Furthermore
unlike other Flooring materials, sharp blades will easily cut the Vinyl Flooringing
so that it may conform to corners, cabinets, and curves.
Vinyl Floorings are not Durable replaced periodically:
Vinyl Floorings may be applied over old Flooring, and are easily cleaned
with a vacuum or a mop with soap and warm water. To the delight of many house holders,
with proper care, many brands do not require waxing. Polyurethane coatings render
a high-gloss finish that emulates a shiny, Waxy surface and generally stays
rather shiny over the years. If dulled, a special Vinyl Flooring finish may be
applied. Vinyl Floorings are not as durable as Ceramic tile and will have
to be replaced periodically.
Vinyl Flooringing Varies in thickness:
As with many household materials, Vinyl sheet and tile Flooring comes in residential
Grade and commercial Grade. Residential Vinyl Flooringing varies in thickness, method
used for imprinting or decorating, and style. Commercial Vinyl Floorings
conform to specifications that require superior durability and stain resistance.
Some commercial Grade Vinyl Flooring is non slip for high public traffic areas.
Raw Materials:
The primary components of Vinyl Floorings include polyVinyl chloride (or Vinyl)
Resins, plasticizers, pigments and trace stabilizers, and a carrier sheet or backing.
The backing may be felt or highly filled paper made from wood pulp and calcium
carbonate. High-gloss surface Vinyl Sheets or Vinyl Tiles have an additional
polyurethane coating applied at the end of the process. The Glue applied to the
back of some Vinyl Tiles is made from Organic Resins.
Design:
The design departments of Vinyl Flooring companies are constantly seeking
new inspiration for successful patterns and colors that will work in sheet and
tile form. The designers work with marketing groups to determine what colors
and styles will capture the public's interest as much as five years from current
production. The designs are transferred from drawing to computer, and mock-ups
of the different patterns are produced in an array of colors. The designs are
then printed off of the computer on full-size paper and in full color.
Full Scale Paper Pattern:
If a full-scale paper pattern is approved for further development, Printing plates
either 18 x 24 in (45.72 x 61 cm) or 24 x 36 in (61 x 91.44 cm) in size are created
by engravers. These plates are then used to print samples of the pattern on
undecorated Flooring (called Gel stock) as prototypes. The wear Layer, or final,
often shiny surface of the sheet Flooring, is applied over the printed pattern,
so the designers have a close approximation of the finished product.
Manufacturing Process:
Making the Vinyl sheet Floor covering:
Vinyl Resins and plasticizers are stirred together in a vat to make a plastisol.
To this plastisol, AZO compound is added. When the Resins, plasticizers, and AZO
compound is heated, the AZO compound decomposes forming nitrogen gas bubbles.
From this mixture, a Vinyl Foam is produced. This Vinyl Foam has the consistency
of pancake batter and can be spread, in a slurry, onto the installation medium
or backing.
Vinyl Resin:
The slurry is laid down on the felt or wood pulp backing via a reverse roll
coater it is poured on and smoothed out. The coated sheet then goes through
an oven where the Vinyl Foam is Gelled. The oven is heated just enough for the
Vinyl resin to absorb the plasticizer and set.
At this point, the Gel is run through a printing press and is impressed with metal
intaglio plates. This impresses the pattern into the Gel sheet, creating the
decorative pattern.
Second Mixing of Plasticizer:
A second mixing of plasticizer and Vinyl are applied on the printed Gel.
The Gel is run through an oven at an even higher temperature. In the oven, the
Vinyl resin absorbs the plasticizer and melts, creating a clear Vinyl. Printed
patterns and inlaid patterns are thus protected under this wear Layer rendering
the pattern durable.
Sheet Vinyl is Ready to be Rolled:
If the pattern requires a matte finish, the sheet Vinyl is essentially ready
to be Rolled. patterns designed with a high gloss finish receive a Layer of
polyurethane coating via rollers. The thickness of this coating is contRolled
with an air knife to insure a consistent thickness.
Polyurethane Coating:
The polyurethane coating is cured photochemically with ultraviolet radiation
lamps and is ready to be Rolled. The matte or high gloss Vinyl sheet Flooring
is then cut to Rolls that are 12 ft (3.66 m) wide x 1,500 ft (457.2 m) long
that can be subdivided based on the needs of retailers.
Quality Control:
As with most manufactured goods, all raw materials are checked to insure they meet
minimum quality standards of production for the company. Felt or paper backings
are checked for thickness and tensile strength. Physical tests are performed
on coatings viscosity, lumpiness, etc. are examined. If all ingredients are
chemically and physically adequate to render a quality product,
the manufacturing can begin.
Intermediary checks are made:
Intermediary checks are made to insure that standards are met. Members of the
production staff perform visual checks on all pieces. If the larger roll does
have contain an imperfection, quality control personnel adjust the computerized
cut map that informs the cutting machines to cut around imperfections.
Sheet Vinyl used by Housing:
Commercial Tiles and sheet Vinyl used by Housing and Urban Development
undergo an array of testing including minimum thickness requirement, durability,
flammability, etc.
Byproducts:
No hazardous materials are unleashed into the environment as a byproduct of the
manufacture of Vinyl Flooring. Waste products are either recycled at the
point of manufacture or sent to a reclaimer for disposal. The heavy metal
stabilizers and pigments used by the Vinyl Flooring industry were replaced
years ago with those considered more environmentally safe. Presently, the
industry is examining ways to utilize waste Vinyl which results from manufacture
as well as recycle or reclaim the scrap Vinyl Flooring discarded by the consumer.
Wishing you all the best,
http://www.seeyourneeds.in
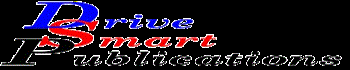